The Evolution and Impact of Knitted Wire Mesh in Modern Industries
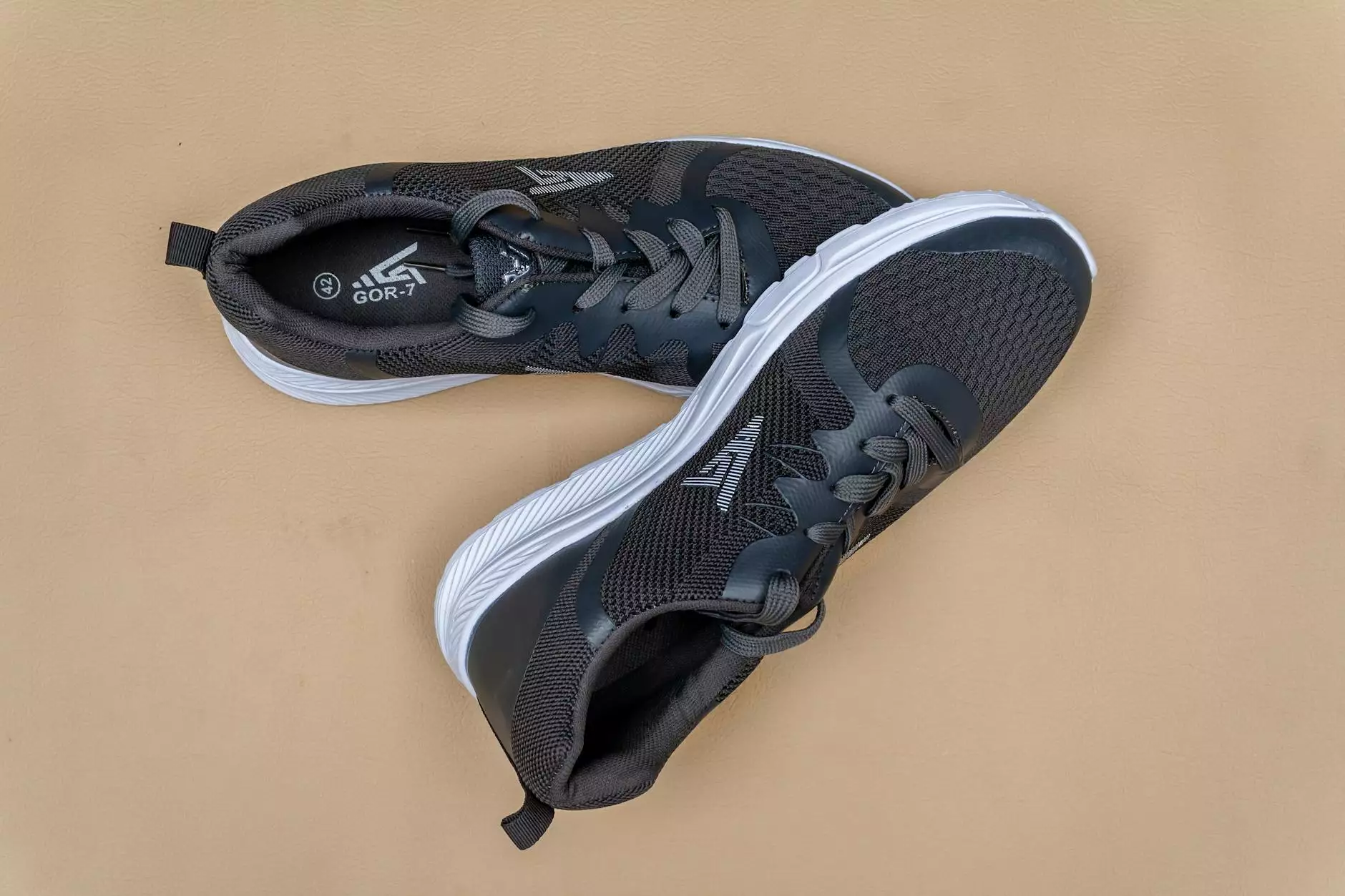
Introduction to Knitted Wire Mesh
Knitted wire mesh is a remarkable material known for its flexibility, durability, and strength. Unlike traditional woven wire mesh, knitted wire mesh consists of intertwined wire strands, resulting in a fabric-like structure that offers unique advantages across various applications. This article delves deeply into the significance of knitted wire mesh, with a particular focus on its applications in electronics and medical supplies.
The Manufacturing Process of Knitted Wire Mesh
The production of knitted wire mesh involves a sophisticated process that begins with the selection of high-quality wire materials. Common wire types include stainless steel, copper, and aluminum, each offering distinct characteristics suitable for different applications.
Key Steps in Manufacturing:
- Wire Selection: Choosing the right type of wire based on the application needs.
- Knitting Process: Utilizing advanced knitting machines that interlace the wire to form a mesh.
- Finishing: Treating the mesh to enhance properties like corrosion resistance, if necessary.
- Quality Control: Ensuring the mesh meets industry standards and specifications.
Applications of Knitted Wire Mesh in Electronics
In the realm of electronics, knitted wire mesh serves several critical functions. Its excellent conductivity and shielding capabilities make it an ideal choice for various electronic components.
Electromagnetic Interference (EMI) Shielding
One of the standout applications of knitted wire mesh in electronics is within the domain of EMI shielding. In our increasingly digital world, protecting sensitive electronic devices from unwanted electrical interference is paramount. The unique structure of knitted wire mesh allows it to effectively block and redirect electromagnetic waves, ensuring optimal performance of various electronic devices.
Thermal Management Solutions
Knitted wire mesh also plays a significant role in thermal management solutions. Its ability to dissipate heat efficiently is crucial in electronic devices where overheating can lead to reduced performance and device failure. By incorporating knitted wire mesh into heat sinks and thermal pads, manufacturers can enhance the longevity and reliability of electronic components.
Resilient Connectors and Fasteners
Additionally, knitted wire mesh is utilized in the production of connectors and fasteners. The elasticity and resilience of knitted wire allow for secure connections without sacrificing flexibility, which is essential for many modern electronic applications.
Impact of Knitted Wire Mesh in Medical Supplies
The use of knitted wire mesh extends significantly into the medical supplies industry, revolutionizing various medical applications. The properties of knitted wire mesh—such as biocompatibility, flexibility, and strength—render it indispensable in several medical settings.
Medical Implants
Knitted wire mesh is increasingly being used in the manufacturing of medical implants. Its ability to conform to anatomical structures while providing structural support is invaluable in applications ranging from orthopedic implants to vascular stents. The mesh allows for fluid movement, bone ingrowth, and ultimately promotes healing and recovery.
Wound Management
In the area of wound management, knitted wire mesh can also be found in advanced dressings and support bandages. The breathable structure of the knitted mesh enables optimal airflow while providing a protective barrier against contaminants, promoting faster healing times.
Filters and Screens in Medical Devices
Knitted wire mesh is an excellent choice for filters and screens used in various medical devices. From ensuring the purity of fluids in IV lines to filtering air in surgical environments, knitted wire mesh provides the necessary durability and efficiency to meet strict medical standards.
Advantages of Using Knitted Wire Mesh
The numerous advantages of knitted wire mesh make it a preferred material in both the electronics and medical industries. Below are some of the key benefits:
- Flexibility: The knitted structure allows for high flexibility, making it adaptable to specific requirements.
- Durability: Resistance to wear and tear ensures a long lifespan in harsh conditions.
- Lightweight: Knitted wire mesh is lighter compared to solid metals, which is advantageous in numerous applications.
- Customizability: Easily customizable in terms of dimensions, wire type, and mesh density, making it suitable for various needs.
- Corrosion Resistance: When treated appropriately, it can resist environmental degradation, extending its usability.
Choosing the Right Knitted Wire Mesh for Your Needs
Selecting the right knitted wire mesh for a specific application requires understanding the intended use, environmental factors, and required properties.
Considerations When Choosing:
- Material Type: Consider the wire material based on conductivity, biocompatibility, and environmental resistance.
- Mesh Density: The configuration should match the needs for filtration, strength, or flexibility.
- Coatings and Treatments: Explore if surface treatments are necessary for specific applications, especially in medical uses.
- Compliance and Standards: Ensure that the knitted wire mesh complies with relevant industry standards and regulations.
Future Trends in Knitted Wire Mesh Applications
As technology continues to advance, the applications of knitted wire mesh are likely to expand and evolve. Emerging fields such as wearable electronics and advanced medical devices open new avenues for innovation.
Wearable Technology
In the electronics sector, the rise of wearable technology necessitates materials that provide comfort without compromising functionality. Knitted wire mesh, with its lightweight and flexible nature, is poised to become a cornerstone in the development of the next generation of wearables.
Smart Medical Solutions
Similarly, in the medical field, there is a growing interest in smart medical solutions that monitor and respond to patient needs in real-time. Knitted wire mesh could serve as a basis for advanced implants and sensors that require both strength and flexibility.
Conclusion
The versatility and advanced properties of knitted wire mesh make it an invaluable material in both the electronics and medical supplies industries. Its unique combination of strength, flexibility, and durability ensures that it meets the challenges posed by modern applications. As we move forward, the potential for knitted wire mesh to enhance product performance and expand into new areas remains boundless. For businesses like nolato.com, leveraging the advantages of knitted wire mesh could lead to significant innovations and improvements in product offerings, positioning them at the forefront of industry advancements.