Leading Innovations in Radiation Shielding: A Comprehensive Guide to Medical Devices Factory
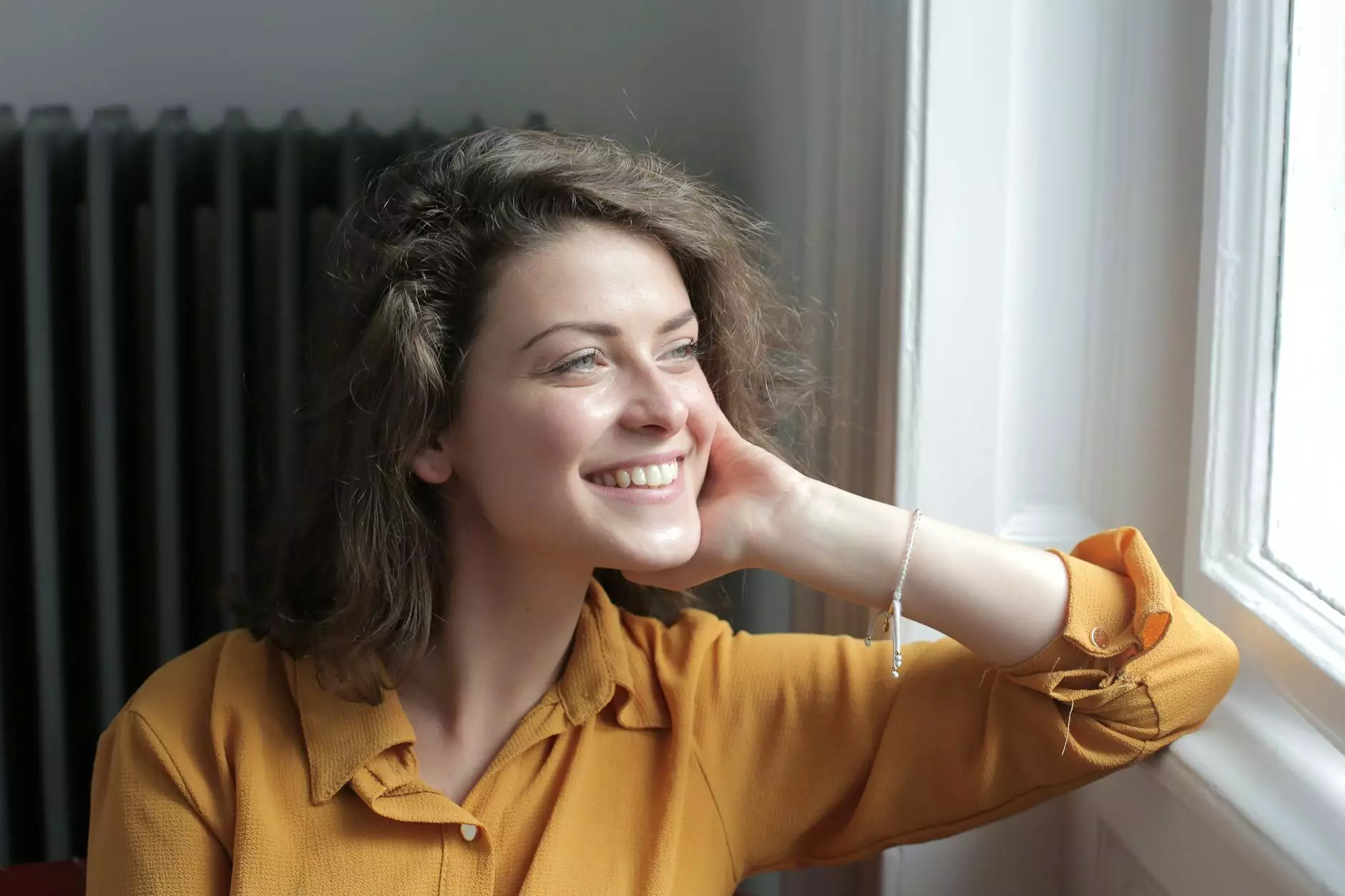
In the realm of modern healthcare, the importance of safety cannot be overstated. As technology evolves, so too does the need for effective radiation shielding materials and devices. Within this context, the medical devices factory has emerged as a critical player, producing essential equipment that mitigates radiation exposure for both patients and medical professionals. This article delves deep into the innovations brought forth by companies like OVM Devices, highlighting their role in revolutionizing healthcare safety.
Understanding Radiation Shielding in Healthcare
Radiation shielding is a crucial aspect of medical practices that involve diagnostic imaging and therapeutic procedures. The primary goal of radiation shielding is to protect individuals from unnecessary exposure to harmful ionizing radiation. As technologies such as X-rays, CT scans, and radiation therapy become more prevalent, understanding the fundamentals of radiation shielding has never been more critical.
Types of Radiation
Radiation can be broadly classified into two categories: ionizing radiation and non-ionizing radiation. Ionizing radiation, which includes X-rays and gamma rays, possesses enough energy to remove tightly bound electrons from atoms, thus creating ions. Non-ionizing radiation, such as microwaves and visible light, does not carry enough energy for ionization. Both types pose distinct challenges in medical settings.
The Role of Medical Devices Factory in Healthcare
Medical devices factories, such as OVM Devices, play a pivotal role in addressing the challenges posed by radiation in healthcare environments. These factories are at the forefront of designing and manufacturing innovative shielding solutions that enhance safety protocols for patients and practitioners alike.
Manufacturing Radiation Shielding Materials
The production of radiation shielding materials involves careful selection of substances that effectively attenuate radiation. Common materials used in the manufacturing process include:
- Lead: A widely recognized material for radiation protection due to its high density, effectively absorbing gamma and X-rays.
- Barium: Often used in composite materials for applications requiring substantial shielding without the excessive weight of lead.
- Concrete: Typically used in facility construction, dense concrete can provide effective protection against radiation while being structurally sound.
- Polymer Composites: These advanced materials combine plastic with heavy metals, providing versatility and lighter options for shielding.
Innovative Radiation Shielding Devices
In addition to raw materials, the medical devices factory is integral to producing a range of innovative radiation shielding devices. The following are some examples:
Radiation Protective Aprons
These aprons are designed for healthcare professionals who frequently work near radiation sources. Made from lead-infused materials, they provide essential protection without hindering mobility.
Mobile Shielding Barriers
These barriers can be repositioned and adjusted according to the specific requirements of the procedure, offering flexible protection solutions in busy medical facilities.
Radiation Shielding Walls
Permanent structures that incorporate lead or lead-equivalent materials, ensuring that operational rooms are sealed off from external radiation exposure.
Importance of Compliance and Standards
To ensure the safety and protection afforded by radiation shielding materials and devices, medical devices factories must adhere to stringent regulations and standards. Regulatory bodies, such as the Food and Drug Administration (FDA) in the United States, enforce compliance with safety protocols that dictate the design, testing, and quality assurance processes in manufacturing.
ISO Certification and Quality Assurance
Many factories seek ISO certification to validate their commitment to quality management and product safety. Compliance with standards such as ISO 13485 ensures that medical devices are consistently produced and controlled to the quality management standards relevant to the manufacture of medical devices.
Future Trends in Radiation Shielding Technology
The landscape of radiation shielding technology is constantly evolving, driven by advancements in materials science and engineering. Here are some future trends that are shaping the industry:
Advanced Materials
Research into lighter, more effective shielding materials continues to be a major focus. Innovations such as graphene composites and nanomaterials show promise for delivering superior protection without the drawbacks of traditional materials such as lead.
Smart Shielding Solutions
Integrating smart technologies, such as sensors that monitor radiation levels in real-time, into shielding devices represent a significant leap forward. These solutions can provide timely alerts and data analytics, allowing medical facilities to improve safety measures dynamically.
3D Printing Applications
3D printing technology is set to revolutionize the production of radiation shielding devices, enabling customized solutions tailored to specific medical environments uniquely and efficiently.
Impact of Radiation Shielding on Patient Care
Effective radiation shielding is directly tied to improved patient care. By minimizing radiation exposure, healthcare providers can enhance patient safety during diagnostic and therapeutic procedures. The implications are profound:
- Reduced Risk of Cancer: Decreasing exposure to radiation significantly lowers the long-term risks of developing radiation-induced cancers.
- Improved Patient Confidence: Patients are more likely to undergo necessary imaging or treatments when they are assured of safety protocols in place.
- Enhanced Staff Safety: Protecting medical professionals from occupational radiation exposure leads to healthier and more capable healthcare providers.
Conclusion
As we move forward in the rapidly advancing field of healthcare, the role of a dedicated medical devices factory such as OVM Devices cannot be overstated. With their commitment to producing high-quality radiation shielding materials and devices, they play an integral role in safeguarding both patients and medical professionals. By adhering to strict regulations and embracing technological innovations, the future of medical safety looks promising, making the healthcare industry not only more effective but also safer for everyone involved.
In conclusion, as we continue to explore new frontiers in medicine, it is imperative that we prioritize safety through responsible manufacturing practices and the use of advanced radiation shielding solutions. The contributions of medical devices factories are undeniable and will remain a cornerstone in the quest for improved healthcare safety.