Understanding Plastic Injection Molding Manufacturers
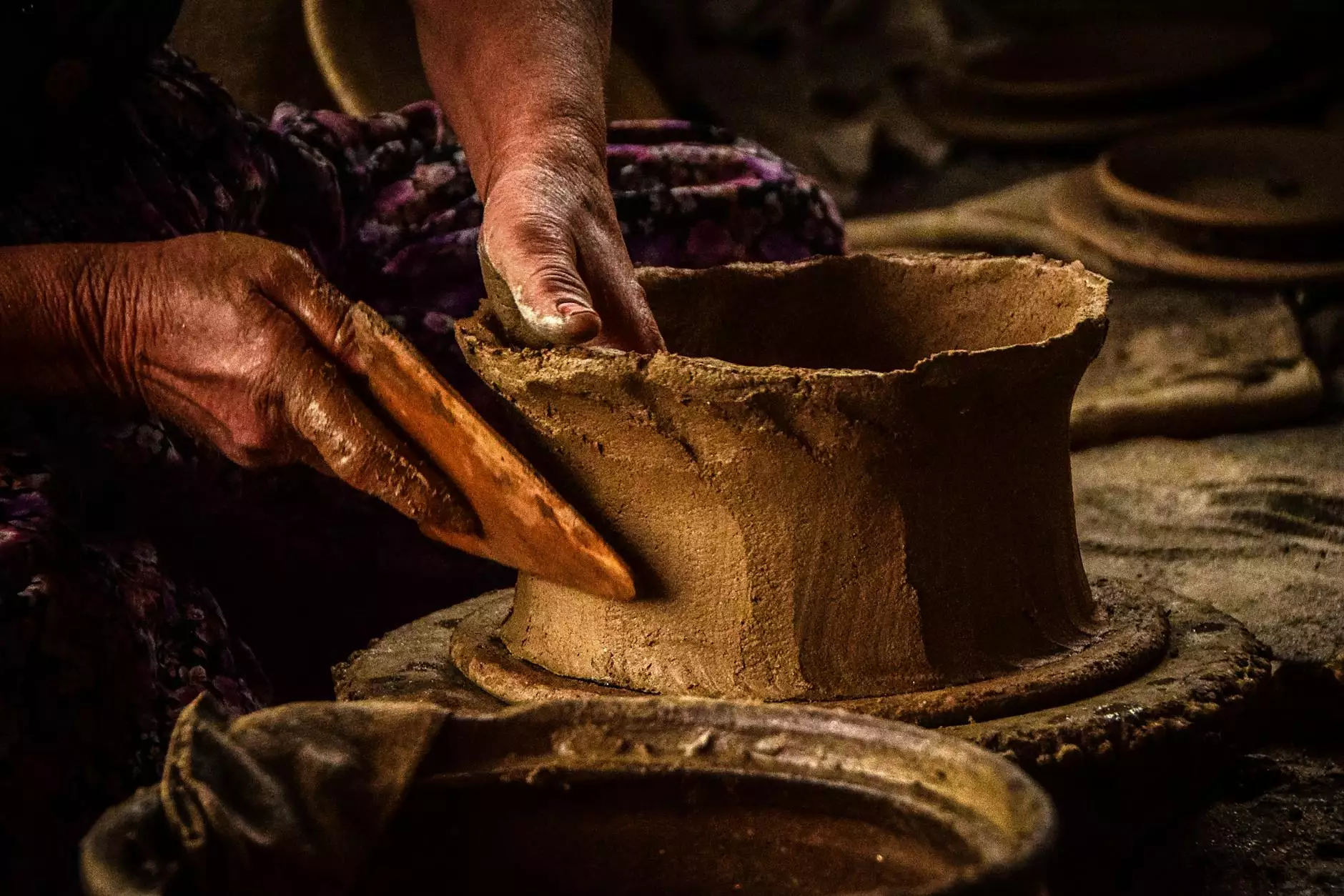
Plastic injection molding has revolutionized the manufacturing landscape, offering unparalleled precision and efficiency in producing high-quality plastic parts. This article delves deep into the realm of plastic injection molding manufacturers, exploring their significance in various industries, the processes they employ, and the benefits they offer.
What is Plastic Injection Molding?
Plastic injection molding is a highly efficient manufacturing process used to create items ranging from complex machine parts to everyday household products. The process involves:
- Melting plastic pellets: Raw plastic material is heated to a molten state.
- Injecting into molds: The molten plastic is injected into specifically designed molds under high pressure.
- Cooling: The injected plastic cools and solidifies, taking the shape of the mold.
- Removing the part: Once cooled, the mold opens, and the plastic part is ejected.
This method is celebrated for its ability to produce large quantities of identical items with high precision, making it a preferred choice for plastic injection molding manufacturers.
The Role of Plastic Injection Molding Manufacturers
Manufacturers specializing in plastic injection molding play a crucial role in various sectors, including automotive, consumer goods, electronics, and medical devices. Their contributions include:
1. Cost-Effectiveness
One of the primary advantages of using plastic injection molding manufacturers is the cost-effectiveness of the process. By producing parts in bulk, manufacturers can significantly reduce per-unit costs. The design flexibility allows custom molds that cater to specific needs, minimizing waste and maximizing production efficiency.
2. Fast Production Times
The injection molding process facilitates rapid production cycles. Once the mold is created, manufacturers can produce thousands of parts within a short time frame. This speed is essential in today’s fast-paced market where time-to-market is critical.
3. High Precision and Quality
With advancements in technology, modern plastic injection molding offers incredible precision. Manufacturers can achieve tolerances of ±0.001 inches, ensuring that the final products meet rigorous quality standards. This level of precision is particularly important in industries like aerospace and medical devices where even minor discrepancies can lead to failures.
Key Industries Served by Plastic Injection Molding Manufacturers
Plastic injection molding manufacturers serve a diverse range of industries, each with unique requirements and standards:
1. Automotive Industry
In the automotive sector, manufacturers create components such as dashboards, bumpers, and interior fittings. The ability to produce lightweight and durable plastic parts contributes to overall vehicle efficiency.
2. Consumer Goods
From toys to kitchenware, the consumer goods industry heavily relies on plastic injection molding manufacturers. The versatility of plastic allows for colorful and intricate designs that appeal to consumers.
3. Electronics
Electronic devices require precise plastic components for enclosures, connectors, and housings. The durability and insulation properties of plastic make it ideal for protecting sensitive electronic parts.
4. Medical Devices
The medical sector demands the highest standards of cleanliness and precision. Plastic injection molding is used to create critical devices and components like syringes, casings, and connectors, ensuring that they meet stringent regulatory requirements.
The Advantages of Working with Plastic Injection Molding Manufacturers
Working with reputable plastic injection molding manufacturers offers several advantages:
1. Expertise and Experience
Established manufacturers possess extensive knowledge and experience in the injection molding process. They understand material properties, design considerations, and manufacturing techniques, which leads to better outcomes.
2. Customization Options
One of the standout features of plastic injection molding is its customization capabilities. Manufacturers can create unique designs tailored to client needs, ensuring that the final product aligns perfectly with the client's vision.
3. Sustainability Practices
Many plastic injection molding manufacturers are adopting sustainable practices to minimize environmental impact. This includes using recyclable materials and implementing energy-efficient production methods, helping companies meet their sustainability goals.
The Process of Choosing the Right Plastic Injection Molding Manufacturer
Selecting the right manufacturer is crucial for project success. Consider the following factors:
1. Industry Expertise
Look for manufacturers with experience in your specific industry. Their understanding of your requirements can lead to better results.
2. Quality Assurance
Ensure that the manufacturer has robust quality control processes in place. Certifications such as ISO 9001 demonstrate a commitment to maintaining high standards.
3. Technological Capabilities
Evaluate the technology and machinery used by the manufacturer. Advanced equipment typically results in higher precision and efficiency.
4. Communication and Support
Reliable communication is key. Choose a manufacturer that provides clear timelines, updates, and support throughout the production process.
Innovations in Plastic Injection Molding
The world of plastic injection molding is constantly evolving. Recent innovations include:
1. 3D Printing in Mold Design
As 3D printing technology advances, manufacturers are incorporating it into the mold design process. This approach allows for rapid prototyping and modification of molds, leading to shorter lead times and enhanced creativity.
2. Use of Sustainable Materials
Many manufacturers are now utilizing bioplastics and other sustainable materials to reduce reliance on fossil fuels. These materials can offer comparable performance while being more environmentally friendly.
3. Automation and Smart Manufacturing
Automation in injection molding processes is on the rise. Manufacturers are integrating smart technologies for real-time monitoring, predictive maintenance, and enhanced production efficiency.
Challenges Faced by Plastic Injection Molding Manufacturers
Despite its advantages, the injection molding industry does face challenges:
1. Fluctuating Material Costs
The cost of raw materials can vary significantly, impacting overall production costs. Manufacturers need to stay informed about market trends and develop strategies to mitigate these fluctuations.
2. Designing for Molding
Designing products for injection molding requires specialized knowledge. Manufacturers must balance aesthetics, functionality, and manufacturability to ensure successful outcomes.
3. Waste Management
Minimizing waste is a critical concern. Manufacturers are continually seeking ways to reduce scrap and recycle materials to enhance sustainability without compromising quality.
Conclusion: The Future of Plastic Injection Molding Manufacturers
The future looks promising for plastic injection molding manufacturers. With ongoing technological advancements, a strong focus on sustainability, and the ever-increasing demand for plastic components across industries, these manufacturers will continue to play a crucial role in modern manufacturing. By leveraging their expertise, embracing innovations, and adapting to market dynamics, they are well-positioned to thrive in the years to come.
For businesses looking for top-tier manufacturing services, partnering with experienced manufacturers like those found at deepmould.net can lead to successful product development and a competitive edge in the market.